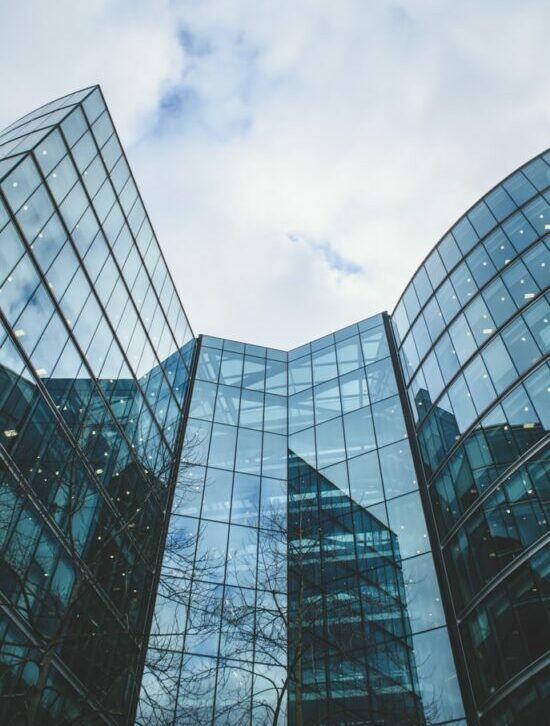
Increased Expenses in Post-COVID Construction: How Project Leaders Can Mitigate Costs for Maximum ROI
Construction costs are rising. Nearly everyone has noticed, from DIY enthusiasts to developers of the most complex construction projects. It’s no secret that COVID presented the industry with major challenges, particularly when it comes to pricing. Labor shortages, supply shortages, and shipping delays are all contributing factors.
In our latest series, we’ve explored the post-COVID economy and how to navigate complex construction projects in a post-pandemic world. In this piece, we will tackle one issue specifically: increased construction expenses and how to navigate the post-pandemic construction material supply chain, rising labor costs, and other expenses so you can maximize your ROI.
Materials
First, let’s consider materials. Over the summer, some construction materials increased by as much as 125 percent. When surveyed this past May, most developers cited rising material costs as the primary factor affecting demand. (Of course, the labor market took a strange turn this summer as well, creating a new problem for developers and owners alike. But we’ll cover that in our next point.)
Lumber prices reached an all-time high in May before slowly dropping till August. Since then, though, prices have climbed skyward again. After six weeks of price increases, lumber is now 50 percent more than it was in August. Experts say pricing and demand are finally starting to balance out, but we can expect steady price increases well into 2022.
Labor
Labor costs are also a concern. There’s still a nationwide labor shortage, and experts say it could get worse before it gets better. In fact, some experts believe the shortage is here to stay, and employees will continue to have the upper hand when it comes to salary negotiations and benefits. Of course, you also have to consider walk-offs — when an employee decides he or she no longer wants the job and leaves without notice. These can drastically delay a project.
Additional Construction Costs
Finally, there are additional expenses that are directly related to COVID.
PPE
Certain jobs require specific PPE for possible COVID exposure and protection. These costs seem minimal on the surface, but navigating the local, state, and federal requirements takes time and planning, and the “minimal” material expenses quickly add up.
Updated Systems and Equipment
The world is much more digital post-pandemic, mostly because of social distancing and the ongoing need for collaboration. Technology gives people the ability to work together on a project, even if they can’t share the same physical space. We use drones for surveys and remote software for meetings and project notes. To keep up with recent changes, you may need to update your systems and equipment.
How to Reduce Expenses and Increase Your ROI
Though there are multiple issues at hand, there are just as many ways to reduce your company’s expenses and increase ROI. Our construction consulting experts suggest:
1. Working with your team.
Start building your project team now if you want to reduce your overall expenses. You can discuss options and concerns with design and pre-construction partners, which helps highlight possible issues and find reasonable solutions. This step helps ensure you stick to your schedule and avoid unnecessary mistakes later.
2. Including Inflation as a Real Cost in Your Project Budget.
You should always include contingency in your financial plan. In the past, construction logic dictated at least 5 percent of your budget be allocated for price inflation and other unforeseen circumstances. With today’s economy, we recommend flexibility when addressing contingency and inflation.
3. Planning ahead and revising as needed.
With every project, it’s best to plan ahead and revise as needed. That’s particularly true post-COVID. Today’s economy is constantly changing, and material prices or labor costs may skyrocket or plummet before your project is complete. You can’t possibly plan for everything, so do the best you can with the information you have on hand and expect revisions later. You can also buy materials early to help reduce the risk of shortages.
4. Paying attention to your contracts.
Increased expenses affect everyone who collaborates on a single project. That means everyone is feeling the squeeze of rising costs and supply chain shortages. Legal teams are recommending you protect yourself with a solid contract that addresses these issues should they arise. The entire team needs to be on the same page in addressing these issues. Sit down with designers, material vendors and contractors to develop a strategy that identifies risk and properly addresses mitigation.
5. Paying attention to your contractors, too.
While you should always try to mitigate your own risks when it comes to material costs, remember to check on your contractors and subcontractors. If they default or file bankruptcy, the whole project is affected. There are legal agreements that help protect owners or developers from these situations, but you can’t fully escape the effects of a delayed or disrupted project. Make sure you also pay your contractors and suppliers promptly, so you are fulfilling your contractual obligations.
Final Thoughts
Thanks to COVID, almost nothing is a certainty in construction. Success is directly correlated with business acumen. By addressing the issues above and planning ahead, you can mitigate your costs and maximize your ROI. You can also partner with a comprehensive construction solutions provider with on-the-ground experience. Contact Willis Construction Consulting to discuss your project and discover how we can help.
Want to learn more? In our next article, we’ll explore the impact of market dynamics on the construction industry in much greater detail. Stay tuned.